What Is Integrated Computational Materials Engineering?
Integrated Computational Materials Engineering (ICME) is a systems-based approach to product design and manufacturing that aims to link materials and processing models into an integrated framework [1]. The grand vision of ICME is that an engineering component and the materials it is made of should be designed in one single integrated process.
Thermo-Calc Software plays a central role in ICME by offering:
Figure 1: Hierarchal chemistry process structure properties performance chain for materials
Figure 2: Comparison of constant handbook value for heat capacity in 316L with calculated temperature dependent heat capacity using the Scheil solidification model. Note: Apparent heat capacity incorporates the latent heat of solidification into the heat capacity.
Figure 3: One example of a generalized material systems design chart, showing some possible Chemistry-process-structure-property linkages. The line colors do not denote anything, but are added for clarity.
Why Thermo-Calc for Integrated Computational Materials Engineering?
Whether you’re designing materials for additive manufacturing or optimizing heat treatment protocols, Thermo-Calc is an essential component of any ICME framework.
Thermo-Calc Software provides:
Webinars on ICME
Learn more about how Thermo-Calc can be used in an ICME framework with this collection of webinars, presented by both Thermo-Calc employees and users who discuss how they use Thermo-Calc in their own work.
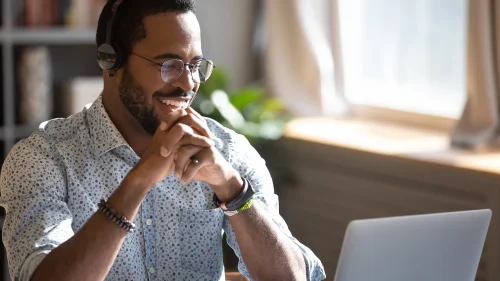
Schedule a Free Consultation
Is Thermo-Calc Right for You?
If you would like to know whether Thermo-Calc is right for you, we invite you to schedule a free consultation.
You can speak directly with one of our experts to discuss whether Thermo-Calc is the right fit for your ICME project.