Applications to Powder Metallurgy
Thermo-Calc can be used to calculate the following as a function of temperature and material chemistry:
Application Examples
Effect of Thermophysical Properties of Liquid on the Atomized Material
Metal powder atomization is a process that uses a fluid, such as gas or water, to break up molten metal into fine powder with a controlled particle size. One of the most important relationships in powder production is the relationship between process parameters and the properties of the liquid metal to the resulting median particle size (D50). In practice, manufacturers often adjust only the process parameters (like gas pressure or nozzle geometry) to control powder size, while overlooking how the properties of the molten metal affect the outcome. By using a modified Kishidaka equation [Urionabarrenetxea et al., 2021], we can relate the D50 particle size to the thermophysical properties of the melt:
The parameters μm (dynamic viscosity of melt; Pa.s), σm (surface tension; J/m2), and ρm (density of melt; kg/m3) are thermophysical properties that can be calculated by most of the Thermo-Calc databases. Therefore, instead of relying on fixed handbook values, users can generate temperature-dependent data to more accurately predict the effect of molten metal properties on powder size. These parameters can be useful for process metallurgists to fine-tune parameters for desirable powder size.
This example compares median powder size variation (normalized) for AlSi10Mg, pure Cu, and 316L stainless steel with respect to changing pouring temperatures (above liquidus temperatures) and assuming other atomization parameters are constant. The calculations use the Al-based Alloys Database, Copper-based Alloys Database, and Steel and Fe-alloys Database, respectively.
Oxygen Inclusions in Stabilizing / Destabilizing Liquidus
The gas atomization process is usually conducted under inert atmospheres (N2, Ar) and using raw materials free from impurities such as O (oxygen). However, if impurities enter the material, they can create inclusions which can lead to clogging of the atomization nozzle. Thermo-Calc can be used to calculate equilibrium phase fractions at different temperatures in order to predict the formation of such inclusions resulting from impurities and to evaluate strategies to mitigate their effects.
This example shows a one-axis equilibrium simulation conducted for a 316L stainless steel containing 200 ppm O. In the top plot, it can be seen that inclusion-free liquidus temperatures increase by 370 ℃ and small amounts of inclusions (spinel) are formed in liquid.
The bottom plot shows that a solution to resolve this issue is to add ~150 ppm of Ca, which forms liquid oxide inclusions and Ca-containing sulfide that floats to the slag, thus preventing clogging. The calculations were made using the Metal Oxide Solutions Database in Thermo-Calc.
Effect of Small Changes in Nominal Chemistry and Pouring Temperature on Atomizing Parameters
The nominal composition for many standard materials often contains chemistry ranges that can be quite wide from a processability point of view. A good example is a commonly used 316L stainless steel, which has a nominal chemistry in the range shown in table.
The resulting thermophysical properties of the liquid metal poured into the atomizing unit are influenced by both the pouring temperature and the nominal chemistry. Changes in these properties then affect both the quality and output of the atomization process.
In the example here, we show the effect of pouring temperature (50-200°C over the liquidus) and nominal chemistry on viscosity and surface tension for 400 different compositions. One plot varies the temperature (green) while the other varies the chemical composition (blue). It can be seen that pouring temperature has a bigger impact on the viscosity whereas the chemical composition has a larger effect on the surface tension. It can also be seen that N positively affects surface tension whereas Cr negatively affects the surface tension. Such calculations can help atomizers visualize the change in the properties of the melt and make corrections to enhance quality and output. The calculations were done using the Steel and Fe-alloys Database and the Liquidus and Solidus Temperature Model in the Property Model Calculator.
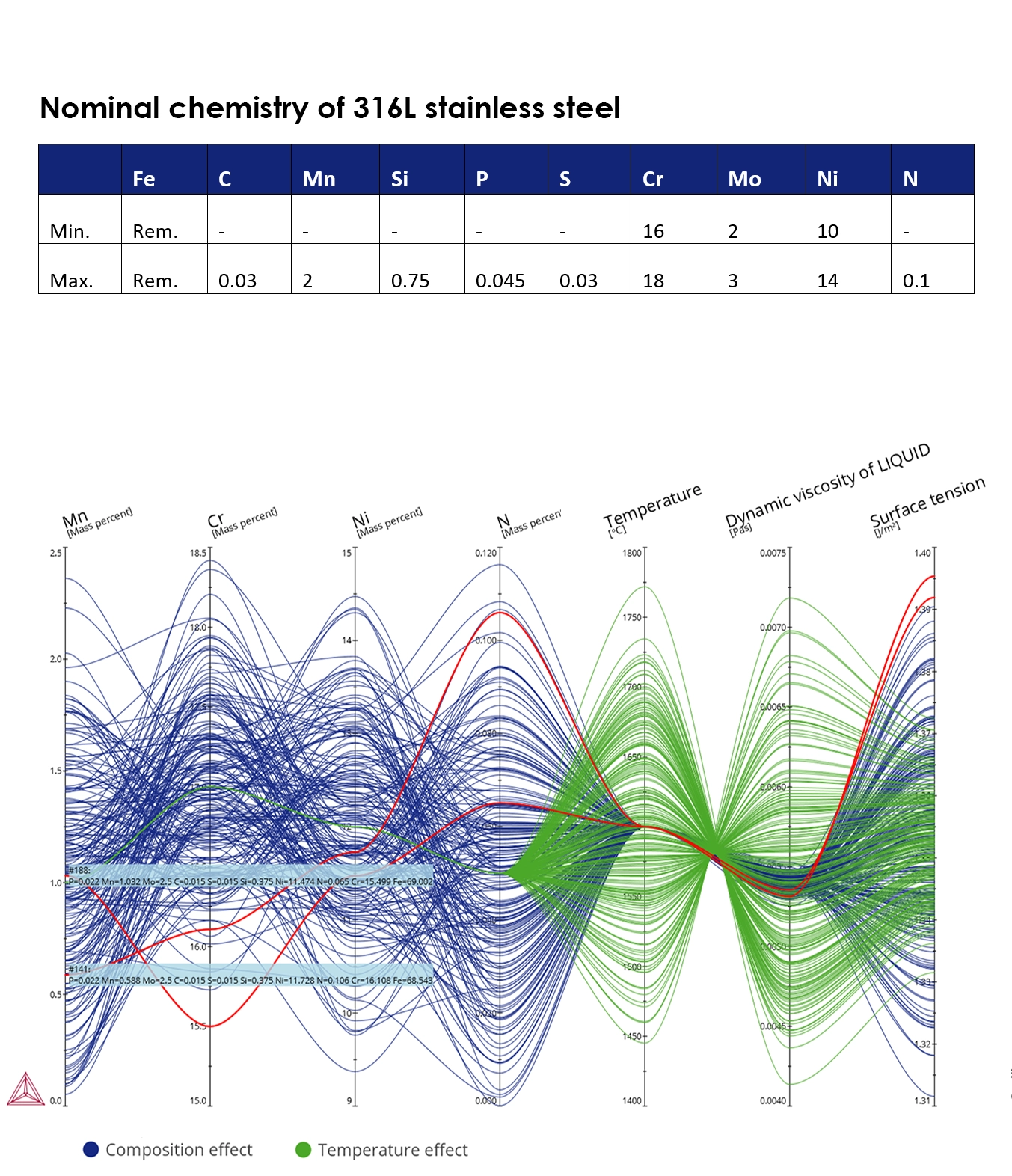
For a better view of the plot, right click and open in another tab.
Gradient Sintering
Once atomized, most metal powder undergoes a process of sintering to consolidate and make nearly fully dense material. In this and the following example, we discuss two aspects of sintering; the aspect of changing microstructure due to diffusional transport of elements during heat treatments (in the case of gradient sintering) or changes in equilibrium phase fractions due to the effects of high pressure (in the case of hot isostatic pressing).
Gradient Sintering is a complex process used by the cemented carbide industry to increase surface toughness away from the cutting edge while increasing hardness at the edge. This process is possible due to the high nitrogen affinity of titanium. During vacuum sintering, cemented carbide is de-nitrided, resulting in an inward diffusion of titanium and dissolution of the carbonitride phase in a surface zone [Ekroth et al.,2000].
The figures show the inward diffusion of Ti during a heat treatment at 1450 ℃ for two hours, which leads to the formation of a carbo-nitride phase [(Ti,W)(C,N)] around the surface zone. The experimental data shows an excellent agreement at time t=7200 s. By using simulations such as these to predict how elements like titanium move and react during sintering, engineers can better control the final microstructure and tailor properties to meet specific performance needs. The calculations were made using the Steel and Fe-alloys Database and the Diffusion Module (DICTRA).
Phase Transformation Due to Pressure During Sintering
Another approach to sintering is hot isostatic pressing (HIP), a method commonly used for densifying powder metallurgical samples by applying high pressure and high temperatures: as high as 2000 bars and 2000 ℃ [Ref:https://quintustechnologies.com/products/material-densification/hot-isostatic-presses/]. The temperature contribution on phase stability is widely discussed in literature, and several of our databases consider these contributions.
In this example, this pressure contribution on ferrite-austenite phase stability in a duplex stainless steel is shown wherein powder samples were HIP and quenched inside HIP chamber (called integrated quenching). The experimentally observed amount of austenite phase (FCC) [Becker et al., 2022] shows a good correlation with Thermo-Calc predictions. This is possible because there is a pressure dependence on molar volumes which affects the Gibbs free energy of the phases, thus affecting their stability. These types of calculations work well with solid phases that have similar compressibility, but is not reliable for liquid/gas phases or at high pressures (>1 GPa). The calculation was made using the Steel and Fe-alloys Database.